Replenishment solutions automation
Smart inventory replenishment automation
Overview
Efficient replenishment is essential for seamless order fulfilment. Without timely stock movement to picking areas, even the best pick strategies can stall, leading to delays, stock-outs, and disappointed customers. Inteq’s replenishment automation ensures materials and products are always in the right place at the right time, supporting fast, accurate picking and continuous fulfilment. Our solutions integrate intelligent, in-house-developed software (IWS) with advanced automation to synchronise inventory movement across your warehouse. This results in fewer bottlenecks, lower stock holding, and more agile operations.
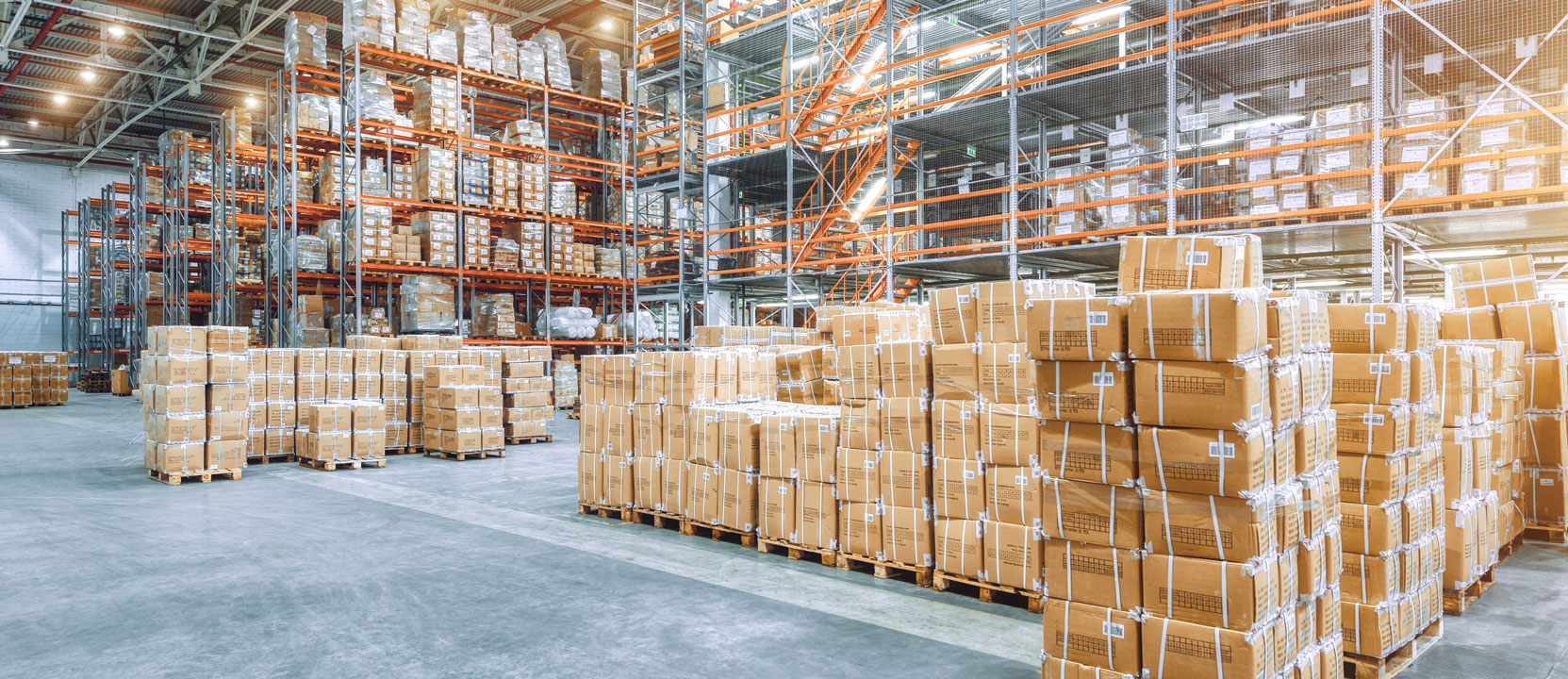
Replenishment
Applications
Inteq’s replenishment automation is built for businesses looking to improve inventory availability, minimise waste, and increase picking efficiency, especially in high-volume or fast-paced environments.
- Manufacturing sites needing a consistent supply of parts for production lines
- Warehouses replenishing pick faces from high-bay or bulk storage
- Facilities spanning multiple floors or buildings with complex material flows
- Operations reducing manual handling to support safer, more ergonomic workplaces
- Businesses adopting lean inventory models with just-in-time delivery
Our solutions
Autonomous Mobile Robots (AMRs)
AMRs handle replenishment autonomously, travelling between storage and forward pick locations with precision and flexibility. They support dynamic scheduling, enabling pick and replenish tasks to happen in the same time window, and they easily adapt to changing layouts. Integrated with IWS, they enable efficient routing, live updates, and optimised resource use.
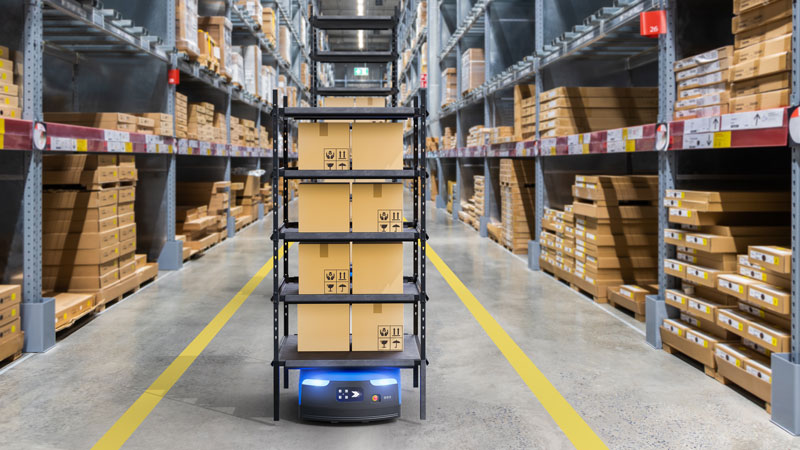
CTU Robot Systems
CTUs are ideal for transporting totes and cartons to flow-rack systems or pick stations. These collaborative robots enhance accuracy and speed by automating pick-up, transport and placement of replenishment stock. When linked with conveyors or automated storage systems, they ensure smooth, coordinated replenishment across your site.
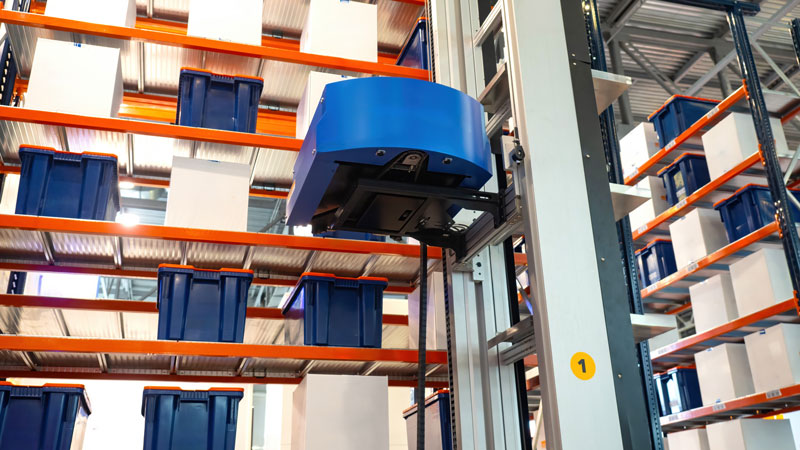
Automated Conveyor Systems
Conveyors are a robust solution for high-throughput replenishment. They transport materials between storage and picking zones with minimal manual handling, supporting continuous flow through multi-level layouts. Features like energy-saving modes, integrated lifts and smart routing deliver dependable performance, especially in complex facilities where timing is important.
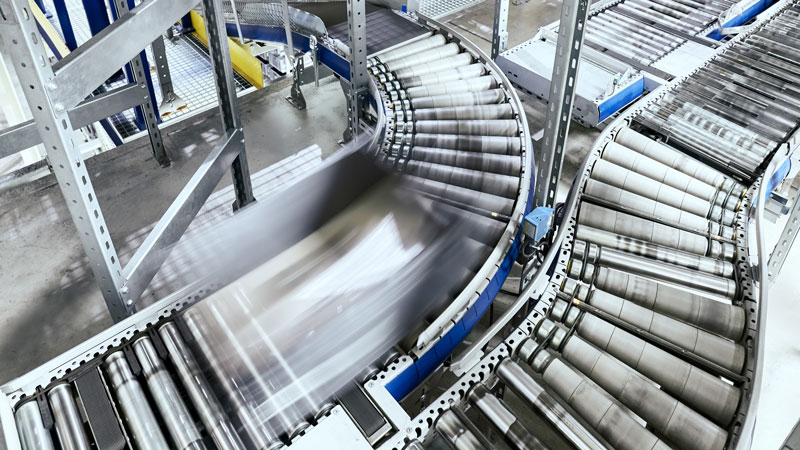
Testimonials
Read what our clients are saying about our solutions.
Discover what we can do for you today.
Get in touch to see how our automation software can streamline your replenishment process.
Contact us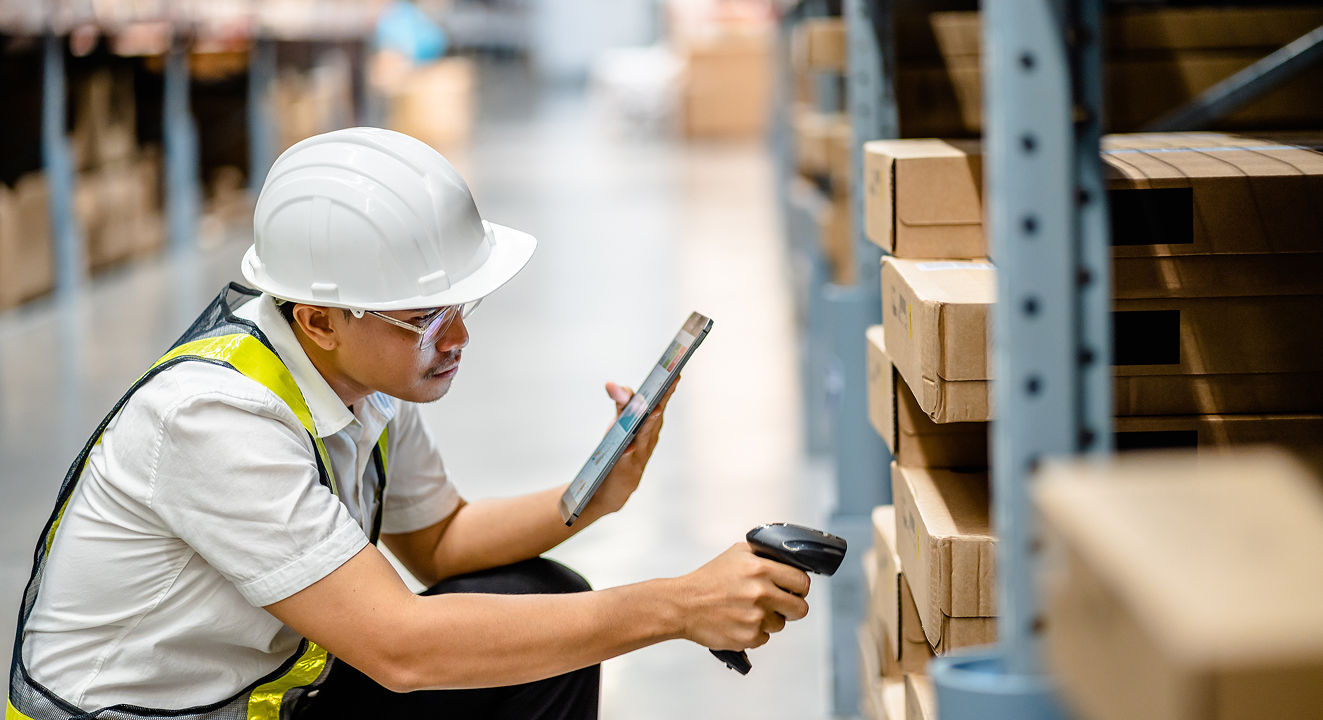